بررسی روشهای جلوگیری از خوردگی میلگرد
خوردگی میلگردهای فولادی و ورق استیل در سازههای بتن آرمه به یک نگرانی مهندسین عمران تبدیل شده است چرا که خوردگی یکی از علل عمده خرابی سازههای بتن آرمه است. این آسیبها از کاهش سطح مقطع میلگردهای فولادی آغاز میشوند و کاهش شکلپذیری و ترکخوردگی و مشکلات چسبندگی بین آرماتور و بتن را به دنبال دارند که منجر به شکست زودهنگام سازه میشوند.
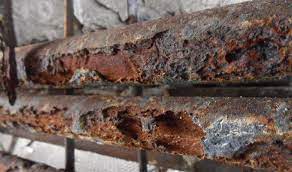
مقاومسازی با میلگردهای frp یکی از روشهای جدید و امیدوارکنندهای است که امروزه برای مقاومسازی سازهها استفاده میشود. هرچند frp در مقایسه با سایر میلگردها بیشتر است ولی در نهایت باعث کاهش هزینههای ترمیم و نوسازی سازهها میگردد. علاوه بر میلگردهای frp استفاده از میلگردهای استنلس استیل و گالوانیزه نیز گام مهمی در جهت کاهش خوردگی بتن است. در ادامه به بررسی روشهای جلوگیری از خوردگی میلگرد خواهیم پرداخت.
روشهای جلوگیری از خوردگی میلگرد در بتن
1 – بهبود عملکرد بتن
اولین موارد تأثیرگذار بر دوام بتن در مقابل خوردگی، نفوذپذیری پایین بتن با میزان سیمان زیاد، کمترین حد کلراید و پوشش بتنی کافی روی میلگردها است. صرف نظر از روشهای دیگر پیشگیری و به تعویق انداختن خوردگی، میبایست ساخت و اجرای بتن با کیفیت مدنظر قرار بگیرد.
پوشش بتنی کافی و مخلوطی با نسبت آب به سیمان پایین میتواند تا حد زیادی نفوذ یون کلر و کربناسیون را به تعویق بیندازد. همچنین مواد افزودنی و مصالح جایگزین سیمان مثل خاکستر بادی، سربارهها، دوده سیلیسی و دیگر مصالح میتوانند اندازه حفرههای داخل بتن را ریزتر کرده یا آنها را مسدود کنند که در نتیجه باعث افزایش پایایی بتن میشوند. در هر صورت عملآوری مناسب بتن هم تأثیر حیاتی روی کیفیت نهایی مورد انتظار بتن ساخته شده دارد.
2 – استفاده از میلگرد با روکش اپوکسی
روکش اپوکسی در یک فرآیند صنعتی در کارخانه روی میلگرد اعمال میشود. ابتدا میلگردها توسط سندبلاست تمیز شده سپس در یک کوره حرارت داده شده و وارد قسمتی میشوند که پودر ریز اپوکسی روی آن اسپری خواهد شد. پودر روی میلگرد داغ میچسبد و قبل از پایان فرآیند، عملآوری و تثبیت میشود. مهمترین قابلیت میلگردهای با روکش اپوکسی، دی الکتریک و عایق بودن آن است به طوریکه یون کلراید نمیتواند از آن عبور کند. همچنین چسبندگی بسیار خوبی به میلگرد دارد و در قسمتهای آسیب دیده توسط خوردگی از فلز جدا نمیشود.
همچنین انعطافپذیر است به طوری که میلگردهای صاف به سادگی در عملیات آرماتوربندی خم شوند. به منظور جلوگیری از آسیب دیدن روکش، عملیات خم کردن باید روی گیرههای مخصوص صورت گیرد. با این حال آسیب به روکش اپوکسی در فرآیند اعمال روکش امری اجتنابناپذیر است که میتواند دلایل مختلفی داشته باشد. حفرههایی روی روکش اپوکسی پس از ساخت به وجود میآید که دلیل آن صیقلی نبودن سطح میلگرد و وجود ناهمگونیهایی در سطح آن است.
در هنگام ساخت و جابجایی میلگردها در کارخانه هم مقداری به روکش آسیب میرسد. برخی از آسیبها هنگام حمل به کارگاه و حین سرهم کردن سبدهای آرماتور در کارگاه به وجود میآیند. سرانجام بتنریزی روی میلگردها و عملیات متراکمسازی هم میتواند منجر به آسیب روکش اپوکسی شود. با توجه به بالا بودن قیمت میلگرد اپوکسی نیاز است پیش از استفاده از این روش نسبت به خطرات احتمالی آن آگاهی کافی داشته باشید.
3 – استفاده از صفحات ضدآب
ورقهای مانع نفوذ آب به طور معمول در عرشه پلهای نوساز در بریتانیا و بسیاری از بخشهای اروپا مورداستفاده قرار میگیرند. همچنین برخی از سازمانهای راه در شمال ایالات متحده و کانادا نیز از این سیستم استفاده میکنند. این صفحات به دو صورت کلی وجود دارند. نوع اول مایعی است که در محل به جامد تبدیل میشود. نوع دوم ورقهایی هستند که به بتن متصل میشوند.
مشکلات اصلی استفاده از صفحات ضد آب، همان مشکلات مطرح در مورد میلگردهای با روکش اپوکسی است، باید آنها را بدون وارد کردن آسیب مورداستفاده قرار داد. آسیب در نوع مایع میتواند به صورت وجود حباب هوا، سوراخ، یا آسیب مکانیکی نمود پیدا کند و در مورد ورق استیل آماده به صورت بریدگی؛ تاشدگی، اتصال بد یا سوراخ در صفحات مشاهده شود. هر دو نوع این صفحات میتواند در هنگام ریختن آسفالت و عملیات متراکمسازی آن آسیب جدی ببینند.
جلوگیری از نفوذ آب و کلراید در خوردگی میلگرد
به منظور جلوگیری از نفوذ آب و کلراید به زیر صفحات باید در اجرا به جزئیات و ریزهکاریها دقت بسیاری داشت. همچنین بسیار مهم است که از وجود زهکشی بین صفحات و دال بتنی و آببندی آن بدون کوچکترین نشتی، اطمینان حاصل کرد. همچنین سیستم زهکشی باید طوری طراحی شود که آب حاوی نمک را روی قسمتهای دیگر سازه نریزد. پلهای زیادی در انگلستان نیاز به تعمیرات اساسی دارند چراکه صفحات ضد آب به کار گرفته شده در آنها، دیگر توان جلوگیری از نفوذ آب و کلراید را ندارند.
استفاده از ورقهای ضدآب نیازمند اندیشیدن جزئیات سازهای بسیاری به منظور ایجاد یک سیستم زهکشی مطمئن و جلوگیری از نشت آب حاوی نمک به زیر صفحات است. این جزئیات بایستی به دقت در هنگام ساخت رعایت و اجرا شوند. یک پوشش خوب نیز برای استحکام صفحات بدون شکسته شدن آنها باید اعمال شود. به کارگیری این صفحات نیازمند حضور گروه متخصص بوده تا بتوان از اجرای صحیح، چسبیدن کامل آن به بتن و آببندی در مرزها مطمئن شد.
4 – پوششهای آببند
بسیاری از سازمانهای راه اروپایی دستورالعملهایی برای استفاده از پوششهای آببند در سازههای بتنی در معرض پاشش نمک یا زهاب ارائه کردهاند. این سیستم کاربردهای ویژهای دارد. در ایالات متحده از آببندها در روی بتنهای ساده پلها هم استفاده میشود. تأثیر آنها در مکانهای تحت عبور ترافیک به اندازه کافی نیست.
مزیت اصلی پوششهای آببند شیمیایی این است که با توجه به بالا بودن قیمت آهن آلات ، آنها نسبت به حفاظت کاتدی، میلگردهای با روکش اپوکسی و دیگر روشهای پیشگیری از خوردگی بسیار ارزانتر هستند. اگر پوشش خوب باشد، دیگر نیازی به نگهداری نیست و لایه ضدنفوذ با عمر طولانی روی بتن قرار دارد. آنها ضربهای به طراحی و کارایی سازه نمیزنند. تنها مشکل آن است که باید مطمئن شد که این مایع بیرنگ به مقدار کافی استفاده شده و مطمئن شویم که سازه را به خوبی پوشانده است.
5 – میلگردهای گالوانیزه
تحقیقات اخیر در آمریکا نشان میدهد که به طور کلی هنگامی که با حمله کلراید مواجه هستیم، گالوانیزه کردن در مقابل استفاده از میلگردهای با روکش ضدنفوذ اپوکسی، انتخاب دوم خواهد بود. عمر میلگردهای گالوانیزه در یک بتن با کیفیت خوب، 15 سال در نظر گرفته میشود. میلگردهای گالوانیزه بیشتر در مقابل کربناسیون مؤثر هستند. میلگردهای گالوانیزه در سازههایی که در معرض خطر کربناسیون قرار دارند با موفقیت استفاده شدهاند.
عمل گالوانیزه کردن به سادگی در اکثر کشورها قابل انجام است. همچنین کیفیت و ترکیب روکش روی دوام و پایایی آن تأثیر مستقیم دارد این میلگردها مشکلات کمتری در هنگام حمل و نقل دارد زیرا روکش از سطح میلگرد محافظت میکند. هنگامی که از ترکیب میلگردهای گالوانیزه و معمولی استفاده شود امکان از بین رفتن روکش گالوانیزه وجود دارد. با توجه به بالا بودن قیمت میلگرد گالوانیزه اگر لازم بود این دو نوع میلگرد در یک سازه استفاده شوند باید از عایقبندی الکتریکی کامل بین میلگردهای گالوانیزه و معمولی مطمئن شد. به کار بردن محافظ الکتروشیمیایی در کنار تسلیحات گالوانیزه با ریسک بالایی همراه است و خوردگیهای بسیار شدیدی امکان دارد اتفاق بیافتد.
6 – میلگرد ضد زنگ
میلگردهای فولادی ضد زنگ در موارد ویژه به کار گرفته شدهاند اما انتخاب بسیار گرانی هستند. یک میلگرد با مغزه فولاد و روکش 1 تا 2 میلیمتر از فولاد ضدزنگ که به تازگی وارد بازار شده است نسبت به فولاد معمولی گرانتر است. اما حدود نصف قیمت میلگرد استنلس استیل خالص را دارد.
برخی از فولادها ضدزنگ مستعد خوردگی حفرهای هستند پس باید از گرید مناسب فولاد ضدزنگ با درصد عناصر آلیاژی نیکل و کروم بالا استفاده شود که مشکلاتی در زمینه کنترل کیفیت و ساخت آن در کارخانه وجود دارد. مشکل استفاده از فولاد ضدزنگ با مغزه آهنی، همچون استفاده همزمان میلگرد گالوانیزه و معمولی است که توضیح داده شد. اتصال الکتریکی بین فولاد ضدزنگ و مغزه آهنی باعث خوردگی سریع در آهن نرمه خواهد شد.
7 – استفاده از بازدارندههای خوردگی
کلسیم نیتریت اصلیترین ماده بازدارنده خوردگی در دسترس است که خوردگی را متوقف میکند و با بتن نیز در عملیات بتنریزی سازگاری دارد. مزیت استفاده از کلسیم نیتریت این است که این مواد میتوانند به مخلوط بتن اضافه شود بدون اینکه تأثیری روی طراحی، ساخت و کارایی داشته باشد.
غیر از این به عنوان یک تندگیرکننده عمل میکند. پس لازم است که از یک کندگیرکننده در طرح اختلاط استفاده شود. محدودیت اصلی این است که به منظور جلوگیری از خوردگی، نیتریت باید به میزان کافی در بتن وجود داشته باشد زیرا در مقابل کلراید مصرف میشود. بنابراین بسیار مهم است که میزان کلرایدی که در طول عمر مفید سازه به آن اعمال میشود محاسبه شود و به مقدار کافی ماده بازدارنده به بتن اضافه شود.
تقویت میلگرد در برابر خوردگی که بر اثر عوامل محیطی مانند وجود اسید، رطوبت و غیره بهوجود میآید، امری ضروری در ساختمانسازی است. در مقاله مربوط به گفتیم که خوردگی میلگردهای فولادی هم میتواند منجر به کاهش استحکام سازه شود. تقویت انواع میلگرد در برابر خوردگی، موضوع اصلی بحث ما در این مقاله است. اینکه چه اقداماتی میتواند مانع بروز چنین مشکلی شود؟ دلایل ایجاد خوردگی میلگرد چیست؟ روش صحیح انبار میلگرد چگونه است و چطور میتوانید آن را در برابر خوردگی تقویت کنید؟ و حتی در صورت ایجاد، چطور زنگزدگی روی میلگرد را برطرف کنید؟ برای اطلاع از روش های تقویت میلگرد در برابر خوردگی این متن را تا انتها مطالعه کنید.
خوردگی میلگرد چگونه اتفاق میافتد؟
گاهی اوقات با قرارگیری میلگرد در محیط با اسید یا رطوبت بالا، فولاد در اثر واکنش شیمیایی یا عوامل محیطی دچار خوردگی میشود. در این حالت آهن موجود در میلگرد به اکسید آهن یا زنگ تبدیل شده که امری نامطلوب است. بروز خوردگی در میلگردها به 3 شرط نیاز دارد: رطوبت، سطح فلزی و ماده اکسیدکننده که بهعنوان گیرنده الکترون شناخته میشود. خوردگی، سطح میلگرد را به شکل پایدارتری یعنی اکسید، هیدروکسید یا سولفید تبدیل میکند.
خوردگی میتواند تأثیرات منفی زیادی روی کارکرد میلگرد بگذارد که با توجه به ، بیتوجهی به شما را با مشکلات فنی و مالی روبهرو میکند. وقتی سازههای فلزی دچار خوردگی میشوند، ایمنی کمتری خواهند داشت و میتوانند منجر به حوادثی مانند ریزش شوند. حتی خوردگی جزئی نیز نیاز به تعمیر و نگهداری دارد. جالب است بدانید طبق مطالعات انجامشده، هزینه سالانه آسیبهایی که مستقیماً ناشی از خوردگی فلزی هستند، تقریباً 2.2 تریلیون دلار در سراسر جهان تخمین زده میشود! البته خوشبختانه با استفاده از روشهای مقابله با خوردگی میلگردها و دیگر مقاطع فولادی، میتوان 25 تا 30 درصد از خوردگی در کل جهان را کاهش داد.
روشهای تقویت انواع میلگرد در برابر خوردگی
ازآنجاییکه مقاومت کل ساختمان به کیفیت میلگردها بستگی دارد، نمیتوان از خوردگی میلگرد چشمپوشی کرد؛ بنابراین لازم است راهکارهایی را برای تقویت میلگرد در برابر خوردگی در نظر گرفت. شما میتوانید با انتخاب درست نوع فولاد، پوشش محافظ، محیط و شرایط نگهداری از خوردگی میلگرد جلوگیری کنید.
برای تقویت میلگرد در برابر خوردگی:
- بهتر است میلگرد را دور از سایر مصالح ساختمانی مانند آجر و چوب نگهداری کنید.
- میلگردهای فولادی را به دور از باران، برف، عناصر نمکی و غیره قرار دهید.
- برای تقویت میلگرد بهتر است بهصورت دورهای یا حداقل قبل از بهکارگیری، سطح آنها را از هرگونه زنگزدگی پاک کنید.
- میتوانید برای تقویت میلگرد، سطح آن را با یک لایه نازک روکش نیکل، کادمیوم یا روی بپوشانید. پوشاندن سطح فولاد توسط روی را گالوانیزاسیون (Galvanization) میگویند که یکی از متداولترین روشها برای مقابله با خوردگی در میلگردهاست.
- در انتخاب میلگرد دقت کنید؛ هرچه نسبت گوگرد و فسفر فولاد بهکاررفته کمتر باشد، در برابر خوردگی مقاومتر خواهد بود.
- استفاده از پوشش رنگ یک روش مقرونبهصرفه برای جلوگیری از خوردگی است. پوششهای رنگی بهعنوان مانعی برای جلوگیری از انتقال بار الکتروشیمیایی از محلول خورنده به فلز زیر آن عمل میکنند.
همچنین میتوان از پوشش پودری بهعنوان راهکاری برای افزایش مقاومت میلگرد استفاده کرد. در این فرآیند، پودر خشکی مانند ترکیبات آکریلیک، پلیاستر، اپوکسی، نایلون و یورتان به سطح تمیز فلز پاشیده میشود. سپس میلگرد گرم شده تا پودر به یک لایه صاف تبدیل شود.
- بازدارندههای خوردگی مواد شیمیایی هستند که با سطح فلز یا گازهای اطراف واکنش میدهند تا از واکنشهای الکتروشیمیایی منجر به خوردگی جلوگیری کنند. آنها با قرار گرفتن روی سطح میلگرد، یک لایه محافظ ایجاد کرده و با غیرفعال کردن سطح فولاد باعث تقویت میلگرد در برابر خوردگی میشوند.
چرا حتما باید زنگزدگی را از روی میلگرد پاک کنید؟
وجود زنگزدگی در سطح میلگرد میتواند باعث خوردگی بیشتر شود. علاوه بر این، اگر میلگرد زنگزده را در بتن قرار دهید، پیوند بین بتن و میلگرد سست شده و در این صورت حتی ترکهای موجود روی بتن نیز به زنگزدگی بیشتر میلگرد کمک خواهند کرد.
برای از بین بردن خوردگی میلگردها چه روشهایی وجود دارد؟
ماهیت خوردگی و درجه خوردگی برای انتخاب روش حذف زنگزدگی از میلگرد اهمیت بسیاری دارد. اغلب حذف خوردگی گسترده هزینه بالاتری دارد. از طرفی استفاده از روشهای مختلف، هزینه متفاوتی را برای کارفرما خواهد داشت؛ پس بهتر است با این روشها بیشتر آشنا شوید.
1. برس کشی میلگرد
برس زدن میلگرد میتواند بهصورت دستی یا با ماشین انجام شود. البته تنها درصورتیکه زنگزدگی جزئی بوده و درکل میلگرد پخش نشده باشد میتوان آن را بهصورت دستی برطرف کرد.
نکته: اگر آرماتور در دال گره خورده باشد، نمیتوان آنها را با ماشین تمیز کرد مگر اینکه از دال خارج شود.
2. استفاده از واترجت یا آب پرفشار
هنگامیکه لایه نازکی از زنگزدگی در سطح آرماتورها وجود داشته باشد، میتوان از واترجت برای تمیز کردن آن استفاده کرد.
3. سندبلاست
از این روش میتوان برای زمانی که میلگرد بهشدت خورده شده باشد استفاده کرد.
- استفاده از مواد شیمیایی
در حال حاضر مواد شیمیایی متفاوتی در بازار برای از بین بردن زنگزدگی میلگردها وجود دارد. بسته به نوع مواد، مرغوبیت و برند تولیدکننده این مواد شیمیایی، هزینه شما متفاوت خواهد بود.
جدا از روشهای بالا، اگر میلگردها بهشدت خورده شده باشند، توصیه میشود که از آنها در برابر خوردگی محافظت کنید. برای این کار بهتر است بلافاصله پس از تمیز کردن، ضدزنگ مناسبی روی میلگردها بزنید. این کار مراحلی دارد که در ادامه روش اجرای دقیق آن را به شما خواهیم گفت.
مراحل تکمیلی تقویت میلگرد برای مقابله با خوردگی
برای مقابله با خوردگی میلگرد بهتر است قبل از بهکارگیری میلگردها مراحل زیر را انجام دهید:
- میلگردها را حدود نیم ساعت در محلول ضدزنگ غوطهور کنید تا زنگارها برداشته شده و سطح روشن میلگردها را ببینید.
مواد لازم جهت تهیه محلول ضدزنگ:
- 50 لیتر اسیدکلریدریک
- 50 لیتر آب
- 5 لیتر بازدارنده
بعدازاین مرحله میلگردها را از محلول خارج کرده و با پارچه مرطوب تمیز کنید.
- در مرحله بعدی باید میلگردها را در محلول قلیایی غوطهور کنید.
مواد لازم جهت تهیه محلول قلیایی:
- یک کیلوگرم پودر قلیایی
- 400 لیتر آب
5 دقیقه به میلگردها اجازه دهید تا در محلول باقی بمانند، سپس آنها را بیرون آورده و تمیز کنید.
- سپس باید ژل فسفات را توسط برس الیافی روی میلگردها بمالید. تقریباً یک ساعت طول میکشد تا این ژل با میلگرد واکنش دهد، پس از طی این زمان، ژل را با شستشوی آب از روی میلگردها بشویید.
- در مرحله بعدی مخلوط نیمه مایع بازدارنده خوردگی را با استفاده از برس الیاف یا غوطهوری روی میلگردها اعمال کنید.
مواد لازم جهت تهیه محلول بازدارنده خوردگی
- 500 سیسی بازدارنده
- یک کیلوگرم سیمان پرتلند معمولی
دقت داشته باشید که این مخلوط باید در همان روزی که آماده میشود استفاده شود. پس از آغشته شدن میلگردها به این مخلوط باید یک روز اجازه دهید تا سطح روی میلگردها کاملاً خشک شود.
- درنهایت محلول آببندی خوردگی را روی سطح میلگردها اعمال کرده و تقریباً 4 الی 5 ساعت صبر کنید تا کاملاً در هوای آزاد خشک شود. پس از خشک شدن کامل، لازم است یکبار دیگر این مرحله را تکرار کنید.
راهکارهای مقابله با خوردگی میلگردها در هنگام انبارش
قطعاً برای شما هم اتفاق افتاده که میلگرد خریدید و به دلایل بسیاری ازجمله متوقف شدن پروژه، تأخیر در اجرا یا حتی سفارش بیشازاندازه مجبور به انبار کردن میلگرد شده باشید. با توجه به ، این میلگردها بخشی از سرمایه شما بهحساب میآیند و شما باید بتوانید به بهترین شکل از آنها نگهداری کنید؛ بنابراین رعایت نکات زیر را به شما توصیه میکنیم:
- بهتر است میلگردها را بالای یک سکوی غیرفلزی برجسته مانند پالت چوبی قرار دهید؛ زیرا سطح زمین و بتن رطوبت را جذب میکنند و منجر به زنگزدگی میشوند.
- میلگردها را با یک لایه محافظ ضخیم بپوشانید و آن را با بلوکهای سنگین (یا هر چیز دیگری که به همان اندازه سنگین باشد) در گوشه انبار محکم کنید. با این کار میزان تماس میلگرد با دیگر عناصر را به حداقل میرسانید و درنتیجه احتمال خوردگی کاهش پیدا خواهد کرد.
- در صورت استفاده از میلگرد گالوانیزه، آن را از تماس با میلگردهای بدون روکش و مواد چوبی دور نگه دارید؛ زیرا تماس بیشازحد با مواد چوبی میتواند سطح میلگرد را لکهدار کند.
- در صورت استفاده از میلگرد فولاد ضدزنگ، از تماس آن با میلگرد فولاد کربنی یا سایر مواد آهنی (آهن) خودداری کنید. اگر این امر اجتنابناپذیر است، مطمئن شوید که میلگرد فولاد ضدزنگ در بالای مواد دیگر قرار گرفته باشد.
طبق گفته وبسایت ، بهتر است “در صورت استفاده از میلگرد گالوانیزه، از تماس با میلگرد بدون روکش و قرار گرفتن بیش از حد در معرض مواد چوبی که می تواند سطح آن را لکه دار کند، خودداری کنید.”
در حال حاضر قوانین سختگیرانهای برای استفاده از میلگرد در ساختمان در نظر گرفته شده و اغلب بازرسان بهسلامت میلگرد بهکاررفته در سازه توجه ویژهای دارند. در این میان خوردگی یکی از مواردی است که میتواند شما را به دردسر بی اندازد و به همین دلیل توصیه میشود در هنگام ساختوساز به تقویت میلگرد در برابر خوردگی بسیار توجه کنید. خوشبختانه در حال حاضر روشهای گوناگونی برای تقویت انواع میلگرد وجود دارد که در مقاله بالا به بیشتر آنها اشاره شد.
یکی از مهمترین عوامل خرابی سازه ها، خوردگی میلگرد مسلح کننده در بتن به شمار می رود. برای مقابله با این موضوع لازم است که تمهیداتی در نظر گرفته شود تا از رسیدن مواد خورنده به میلگرد جلوگیری شود یا مقاومت شیمیایی میلگرد در برابر مواد خوردنده افزایش یابد. بر همین اساس روش های مختلفی برای محافظت بتن مسلح از پدیده خوردگی توسعه یافته اند.
وجود مقدار زیادی از هیدروکسید کلسیم و عناصر قلیایی مانند سدیم و پتاسیم در بتن تازه موجب شده که محیط بتن یک محیط بسیار قلیایی شود. در نتیجه این عمل، بر روی سطح میلگرد لایه نازکی از اکسید به وجود می آید و در نهایت باعث خوردگی میلگرد می شود. در صورتی که اقدامات لازم جهت محافظت از سازه های بتنی انجام نگیرد، بر اثر عوامل مختلفی همچون حضور یون های خورنده، رطوبت، اکسیژن و عوامل محیطی سازه سطح میلگرد شکسته می شود.
راه کار جلوگیری از خوردگی میلگردها
یکی از روش های مناسب برای جلوگیری از خوردگی میلگرد در محیط های مرطوب و آسیب پذیر، تقویت میلگرد با مواد مناسب می باشد. معمولا روش های تقویت میلگرد در برابر خوردگی، پیوند یافته می باشند. به عنوان مثال، ایجاد خاصیت ضد خوردگی با استفاده از مواد اسیدی یا قلیایی و پوشش اپوکسی پیوند یافته است.
اصل اساسی این فرآیند یعنی تقویت میلگرد جهت جلوگیری از خوردگی، جلوگیری از واکنش بین یون های کلراید و تقویت میلگرد است. به این ترتیب، زمانی که لازم است برای دستیابی به مواد مخرب و خوررنده به میلگرد، افزایش یافته و در نهایت دوام سازه به طور قابل ملاحظه ای اضافه می شود.
ایجاد خاصیت ضد خوردگی با استفاده از مواد اسیدی و قلیایی
فرآیند ایجاد خاصیت ضد خوردگی با استفاده از مواد اسیدی و قلیایی جهت تقویت میلگردها، بعد از برش و خم کاری میلگرد می باشد که این کار در یک محل ایزوله انجام می گیرد. در واقع میلگردهای تقویت شده در یک محیط ایزوله روی تکیه گاه های چوبی یا سنگی قرار داده شده و یک لایه محافظ به ضخامت حدود ۰.۱ میلیمتر بر روی آن اجرا می شود.
فرآیند تقویت میلگرد برای محافظت در برابر خوردگی با استفاده از مواد اسیدی و قلیایی را می توان به صورت زیر خلاصه کرد:
میلگردهای تقویت شده در حدود ۱۵-۳۰ دقیقه در محلول ضد زنگ غوطه ور می شوند تا فرسودگی ها برداشته شده و میلگردهایی با سطحی صیقلی به وجود آیند.
محلول ضد زنگ با مخلوط کردن محلول مهار کننده به همراه اسید هیدروکلریک و آب تهیه می شود. نسبت مخلوط در این محلول، ۵ لیتر ضدزنگ و ۵۰ لیتر اسید هیدروکلریک می باشد که برای تولید ۱۰۰ لیتر محلول ضد زنگ، می توان ۵۰ لیتر آب استفاده کرد.
سپس میلگرد ها از محلول خارج شده و با پارچه مرطوب تمیز می شود.
پس از این مرحله، میلگردها در محلولی که با مخلوط کردن پودر قلیایی با آب تولید شده، غوطه ور می شود. در این محلول، ۱ کیلوگرم پودر باید با ۴۰۰ لیتر آب مخلوط شود و میلگردها باید ۵ دقیقه در این محلول باقی مانده و سپس تمیز و خارج شوند.
سپس ژل فسفاتی بلافاصله با استفاده از یک برس روی سطح میلگردها کشیده می شود. این ژله بهتر است به مدت ۴۵ الی ۶۰ دقیقه با سطح میلگرد واکنش داده و سپس با شستشو در آب یا به وسیله یک پارچه مرطوب تمیز شود.
محلول ضد خوردگی با استفاده از یک برس روی سطح میلگرد اعمال می شود.
محلول ضد خوردگی با سیمان پرتلند معمولی به نسبت ۵۰۰ سی سی به ۱ کیلوگرم، مخلوط شده و یک دوغاب تهیه می شود. سپس این دوغاب با برس زدن روی سطح میلگرد اعمال می شود. تمام مراحل فوق باید در همان روز اعمال شود و به میلگرد اجازه داده شود تا به مدت ۱۲ الی ۲۴ ساعت خشک شود.
در نهایت و در مراحل آخر، از محلول آب بندی استفاده می شود.
محلول آب بندی، جهت جلوگیری از خوردگی روی سطح میلگرد، اعمال می شود. این پوشش بعد از ۴ ساعت خشک شدن، دوباره تکرار می شود.
ایجاد خاصیت ضدخوردگی با مواد اسیدی
ایجاد خاصیت ضد خوردگی به کمک پوشش اپوکسی فیوژنی
فرآیند اجرای پوشش اپوکسی فیوژنی بر روی میلگردها، طبق استاندارد IS:13620 انجام می شود که توسط یک کمیته تخصصی در کارخانه ها انجام می گیرد. در صورت استفاده از روکش اپوکسی، باید جزئیات بیشتری در نظر گرفته شود که این جزئیات را می توان در استاندار IS:13620 یافت.
مراحل فرآیند اجرای پوشش اپوکسی فیوژنی بر روی میلگردها، شامل مراحل زیر است:
سطح میلگرد فولادی را با استفاده از لوازم سایشی تمیز کنید تا سطح صاف و تمیزی حاصل شود. سطح میلگرد باید روشن، صاف و عاری از هر گونه زنگ زدگی و مواد خارجی باشد.
در اسرع وقت باید روکش مورد نظر را روی سطح تمیزشده استفاده کنید. زیرا حداکثر مدت زمان تمیز کردن تا شروع کار و استفاده از روکش هشت ساعت است.
این پوشش باید به عنوان پودر خشک با نیروی الکتریکی، اسپری شود که با استفاده از یک تفنگ اسپری الکترواستاتیک بر روی میلگردهای فولادی پاشیده می شود.
پودر می تواند به صورت گرم یا سرد استفاده شود.
میلگرد تقویت شده باید در معرض یک عملیات حرارتی مشخص توسط سازنده قرار گیرد. هم چنین برای جلوگیری از هرگونه شکستگی و یا نقایص دیگر، دما نیز باید کنترل شود.
۹۰ درصد از کل ضخامت پوشش تقویتی باید بین ۰.۱ تا ۰.۳ میلیمتر باشد.
این پوشش باید پس از خشک شدن، مورد بازرسی قرار گیرد و عاری از هرگونه سوراخ، حفره، آلودگی، ترک و آسیب دیدگی باشد.
ایجاد خاصیت ضد خوردگی با استفاده از پوشش بتنی
پوشش بتنی در دو نوع سطحی و نفوذی است. پوشش نفوذی عملکرد بهتری نسبت به پوشش سطحی دارد به طوری که گردش اکسیژن را محدود نمی کند، اما از ورود مواد اضافی جلوگیر می کند. عملکرد پوشش نفوذی به طوری است که وارد حفره های بتن می شود که هم از داخل بتن محفظت کرده و نیز از سطح رویی آن محافظت می کند.
پوشش سطحی به این صورت است یک لایه پلاستیکی روی بتن کشیده می شود که از عبور مواد شیمیایی از حفره های بتن جلوگیری می کند.
انواع پوشش بتنی
انواع پوشش های بتنی عبارتند از:
پوشش نواری شکل از جنس پلاستیک
پوشش بتنی به مدد ساروج
انواع پوشش های رزینی
پوشش بتنی معروف به شات کریت
ایجاد خاصیت ضد خوردگی با استفاده از گالوانیزاسیون
با ایجاد یک لایه روی بر میلگردها تا میزان زیادی از خوردگی و اکسید آهن آن ها می توان جلوگیری کرد، استفاده از این روش بسیار متداول است و به آن اندودشدن یا گالوانیزاسیون می گویند. این فرآیند از طریق اندود کردن فولاد در حوضچه روی صورت می گیرد.
روش های از بین بردن خوردگی میلگردها
معمولا برای از بین بردن خوردگی میلگردها از روش هایی استفاده می شود که برخی از آن ها به صورت زیر است:
برس کشی میلگرد
استفاده از واترجت یا آب پرفشار
سندبلاست
استفاده از مواد شیمیایی
خوردگی میلگرد از جمله عواملی است که موجب کاهش تقویت سازه و عمر آن می گردد. بنابراین لازم است عملیاتی انجام شود تا میلگردهای موجود در بتن کمتر دچار پوسیدگی و خوردگی شوند. بر همین اساس روش های مختلفی برای محافظت بتن مسلح از پدیده خوردگی توسعه یافته اند. از جمله عواملی که تا حدی از این خوردگی جلوگیری می کند، شامل استفاده از مواد اسیدی و قلیایی، پوشش اپوکسی فیوژنی، پوشش بتنی و گالوانیزاسیون هستند که به طور مفصل در این مطلب شرح داده شد.
سوالات متداول روشهای محافظت و تقویت میلگرد در برابر خوردگی
مهترین عامل خرابی سازهها چیست؟
یکی از مهمترین عوامل خرابی سازهها، خوردگی میلگرد مسلح کننده در بتن می باشد.
راه جلوگیری از خوردگی میلگرد چیست؟
روشهای جلوگیری از خوردگی میلگرد در محیط های مرطوب و آسیب پذیر، تقویت میلگرد با مواد مناسب می باشد.
فرآیند اجرای پوشش اپوکسی فیوژنی بر روی میلگردها بر اساس چه استانداردی انجام می شود