خط تولید سرامیک
در این مطلب اطلاعاتی در زمینه خط تولید اروزیل و همچنین آشنایی با تولید کاشی در اختیار قرار می گیرد ، امیدوارم تا انتهای مطلب همراه ایران صنعت باشید.
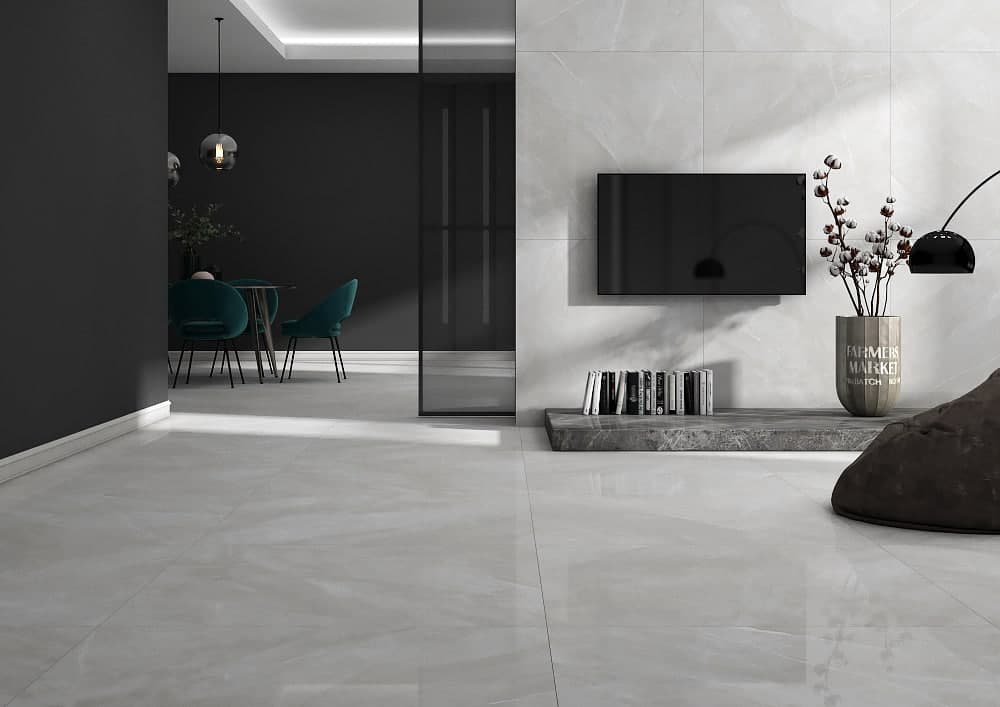
طبق تعاریف قدیم، یک فرآورده سرامیکی محصولی است از دوغاب (مخلوطی از خاک و آب) که در یک محیط گرم و خشک و در نهایت در آتش سخت میگردد.
مطابق تعاریف جدید سرامیکها عبارتند از اشیاء جامدی که اجزاء اصلی تشکیل دهنده آنها مواد معدنی غیر فلزی بوده که ابتدا شکل گرفته و سپس در حرارت سخت میگردند.
کشور ایران با تاریخ و تمدن کهن در هنر و صنعت و برخورداری از ذخایر متنابهی از مواد اولیه از دیر باز با عنوان بستری مناسب برای صنعت کاشی و سرامیک مطرح بودهاست. تولید کاشی سرامیکی در این سرزمین از مراحل بسیار اولیه و با روشهای ابتدایی از حدود ۱۲۵۰ سال قبل از میلاد مسیح با تولید انواع آجرهای لعابدار، کاشیهای تزیینی و مینا آغاز شدهاست.
سرامیکها در چهار خانواده بزرگ به شرح زیر طبقه بندی میشود:
:: فرآورده های ویژه و سرامیکهای تکنیکی و پودر سیلیس
:: دیر گدازها
:: فرآورده های زمخت
:: فرآورده های ظریف
خانواده فرآورده های ظریف به چهار دسته زیر تقسیم میشوند:
:: ظروف خانگی
:: سرامیکهای بهداشتی
:: کاشیها
:: مقرء ها و عایقهای الکتریکی
دستگاه های درگیر در فرآیند تولید: ( اصلی)
۱-سنگ شکن
۲-باکسفیدر
۳-بالمیل دوغاب و لعاب
۴-اسپری درایر
۵-دستگاه پرس
۶-کوره های رولری و تونلی
۷-خط لعاب و دکور زنی
۸-بسته بندی و درجه بندی
به طور خلاصه پروسه تولید کاشی را در شماتیک زیر مشاهده می نمایید :
۱- آماده سازی مواد اولیه بدنه کاشیها:
مواد اولیه عمده بدنه کاشیها خاکهای مختلفی است که از معادن کشور تأمین میشود.
به طور کلی این مواد شامل سه دسته زیر میباشند که بر اساس نقش آنها در بدنه طبقه بندی گردیدهاند:
:: مواد اولیه پلاستیک
:: پر کنندهها (فیلرها Fillers)
:: کمک ذوبها یا گداز آورها (Fluxes)
۱.۱. مواد پلاستیک
رسها مهمترین، پر مصرفترین و قدیمیترین مواد اولیه در صنعت سرامیک میباشند و اصولاً صنعت سرامیک حیات خود را مدیون رس میباشد. اصطلاح رس به کلیه خاکهائی اطلاق میشود که دارای خاصیت پلاستیسیته میباشند و خاصیت پلاستیسیته به صورت زیر تعریف میشود:
خاصیتی است که یک ماده را قادر میسازد تا در اثر یک نیروی خارجی بدون شکست و گسستگی تغیر شکل داده و بعد از حذف یا کاهش نیرو همچنان حالت خود را حفظ نماید. خاک رس به خاکی گفته میشود که بخش عمده آن کانیهای رسی میباشند. کانیهای رسی از تجزیه و هوازدگی سنگهای آذرین (سنگهایی حاصل از انجماد ماگما) مثل گرانیت، پگماتیت گرانیت و… به وجود میآیند. گرانیت ها از سه کانی میکا، کوارتز و فلدسپات با نسبتهای تقریباً برابر تشکیل شدهاند. در بین این سه کانی، فلدسپات در برابر آب و هوازدگی از همه ضعیفتر و ناپایدارتر بوده و پس از میلیونها سال به کانیهای رسی تبدیل میشود.
بنابراین در خاکهای رسی علاوه بر کانی رسی، کانیهای کوارتز و میکا و حتی فلدسپات به مقدار زیادی وجود دارد و هر چند میزان کانیهای رسی بیشتر باشد خواصی نظیر پلاستیسیته در حد بالاتری قرار خواهد داشت.
مینرالهای (Minerals) رسی را بر اساس ساختمان مینرالی به گروههای مختلفی تقسیم بندی میکنند که از بحث ما خارج میباشد اما جهت یاد آوری مهمترین کانیهای رسی مصرفی در این صنعت شامل کائولیت ها، مونت موری لونیت ها، ایلیتها، لوئیزیتها و… میباشند.
اما دلایل عمده استفاده از رسها در این صنعت به شرح زیر میباشد:
به علت وجود بنیانهای مولکولی Sio2,Al203 در ساختمان رسها بعد از پخت فازهای بسیار سخت سیلیکاتی را تولید نموده و موجب افزایش مقاومت در محصولات میگردند. کانیهای رسی با سختی تقریباً یک موجب ورود این بنیانها در فرمول بدنه میگردند. در حالی که اگر بخواهیم همین مواد را به طور خالص که بنام کوارتز و کراندم با سختی به ترتیب ۷ و ۹ میباشند در فرمول وارد کنیم سایش آنها تقریباً غیر ممکن و بسیار هزینه بر خواهد بود.
بنابراین هزینه خریداری رسها بسیار پایینتر از مواد دیگر است.
در بین کانیهای موجود در طبیعت رسها بسیار ریز دانهترند و گاهاً میلیونها برابر کوچکترند و از طرفی به واسطه شکل لایه ای موجب ایجاد یک دوغاب هموژن میگردند که زمان ته نشینی آن بسیار طولانی است در حالی که مواد دیگر چنین خاصیتی را ندارند.
رسها به واسطه خاصیت پلاستیسیته موجبات شکل پذیری آسانتر محصول را فراهم میآورند و از طرفی به واسطه چسبندگی بالایی که دارند میتوانند باعث افزایش استحکام خام و خشک و کاهش ضایعات گردند و این امکان را فراهم آورند که بر روی محصول دکورها و چاپهای مختلف اعمال گردد.
۱.۲. :
مواد غیر پلاستیکی هستند که به بدنه اضافه میگردند و معمولاً دارای نقطه ذوب بالا و مقاومت شیمیایی خوبی بوده و مهمترین وظیفه آنها جلوگیری از تغییر شکل بدنه در طول پخت، انبساط حرارتی مناسب و کنترل انقباضتر به خشک و خشک به پخت میباشد.
علاوه بر این موارد پر کنندهها در تعین تخلخل و رنگ (سفیدی) بدنه اتصال مناسب لعاب و بدنه و اصلاح بافت بدنه خام و… نیز نقش بسیار مهمی را ایفا مینمایند. مهمترین و رایجترین پر کنندهها در صنعت سرامیک سیلیس و آلومین (کروندوم) میباشد. مهمترین نقش سیلیس تشکیل فازهای سیلیکاتی سخت و حتی فلز مایع را در حین پخت دارد که باعث چسبیدن ذرات دیگر میشود. مصرف آلومین علاوه بر نقشهای مذکور باعث میشود که بتوان محصول نازکتر تولید نمود و نیز باعث کاهش تغییر شکل محصول در حین پخت و کاهش ترکهای پخت و بهبود و رنگ فراورده و نیز افزایش مقاومت شیمیایی میگردد.
۱.۳. گدازآورها:
گدازآورها موادی هستند که به جهت کاهش نقطه ذوب بدنه و یا لعاب مصرف بالایی در این صنعت دارند. گدازآورها در هنگام پخت بدنه ذوب گردیده و در هنگام سرد شدن فاز شیشه ای را در بدنه به وجود میآوردند که کلیه بلورهای موجود در بدنه پخته در بر گرفته و بدین ترتیب موجب افزایش استحکام محصول نهایی میگردند.
مهمترین گدازآورهای بدنه، اکسید های سدیم، پتاسیم، کلسیم و منیزیم میباشند که جهت تأمین آنها از فلدسپاتهای سدیک، پتاسیک و کلسیک استفاده میشود.
اما غیر از این مواد، موادی نظیر کربناتها مثل کلیست و دولومیت نیز در بدنه کاشیهای دیواری مصرف میشود که نقش تأمین جذب آب را در این کاشیها ایفا مینماید.
منظور از آماده سازی مواد اولیه اعمالی است که بعد از ورود مواد اولیه به کارخانه و قبل از توزین و اختلاط آنها، انجام میگیرد این مرحله اولین مرحله در خط تولید کارخانجات بوده و به طور عمده شامل خرد کردن و آسیاب نمودن مواد است.
آماده سازی مواد اولیه بسته به نوع مواد و اندازه آنها متفاوت است.
در مرحله خردایش که بیشتر در مورد مواد سخت و دانه درشت بکار میرود توسط یکسری از سنگ شکنهای مختلف مواد درشت به مواد ریز تبدیل میگردد. سنگ شکنهای مختلف رایج در صنعت سرامیک فکی، چکشی، مخروطی و غلطکی و دوار و…میباشد.
در مرحله آسیاب کردن عمدتاً از آسیابهای گلوله ای استفاده میشود.
آسیابهای گلوله ای، استوانه های بزرگی از جنس فولاد هستند. ابعاد استوانه به نحوی است که تقریباً طول استوانه برابر قطر آن میباشد و جدارهای این آسیابها به وسیله آستری از جنس لاستیک یا جنس آجر های آلوبیتی پوشیده شده است.
این استوانهها حول محور خود که موازی سطح افق است گردش مینمایند. همچنان که از نام آسیاب گلوله ای نیز مشخص است در داخل این آسیابهای گلولههایی وجود دارد که هنگام گردش آسیاب با مواد اولیه موجود در آن برخورد نموده و بدین وسیله باعث خرد شدن و سایش آنها میگردند.
جنس گلولهها عمدتاً از آلوبیت و در برخی از مواد گلوله های طبیعی سیلیسی (فلینت) میباشد.
مقدار گلولهها، شکل و کرویت و دانه بندی و خصوصاً سختی آنها عامل بسیار مهمی در کیفیت سایش مواد میباشد.
در آسیابها مواد به اضافه آب و مقادیر کمی روان ساز نظیر سیلیکات سدیم، تری پلی فسفات سدیم Tpp، کربنات سدیم و پس از مدتی سایش با دور مشخص و سرعت مشخص تبدیل به دوغ آب میگردد. مقادیر این مواد دقیقاً از قبل تست شده و مشخص شده میباشد.
نکته قابل توجه اینکه در هر یک از مراحل آماده سازی بازرسیها و کنترلهای لازم جهت عدم عدول از استاندارد های کارخانه ای صورت میگیرد.
کیفیت مواد ورودی، درصدهای اختلاط، مشخصه های محصول سنگ شکن و خصوصاً مشخصه های دوغاب پس از آسیاب نظیر دانسیته، ویسکوزیته و دانه بندی دقیقاً کنترل میشود.
۲-:
جهت آماده سازی پودر از دوغاب از خشک کنهای افشان یا پاشنده یا اسپری درایر استفاده میشود. دوغاب حاصل از آسیابها پس از دپو در مخازن دوغاب که موجب هموژن شدن دوغاب و بهبود خاصیت پلاستیسیته آن میگردد وارد مخازن دوغاب اسپری درایر میگردد. پمپهای پیستونی با فشار نسبتاً بالا دوغاب را به محفظه استوانه ای اسپری درایر که داغ میباشد اسپری نموده و دوغاب پس از برخورد با هوای داغ و تبخیر آب به پودر با رطوبت مشخص و دانه بندی مشخص تبدیل میشود. هوای محفظه و بخار آب پس از عبور از سلیکن ها و گردگیری از خروجی اسپری درایر خارج میشود و محصول آن که پودر میباشد از زیر قلف بر روی نوار نقاله ریخته و در داخل سیلوهای پودر دپو میشود.
کیفیت پودر به عوامل زیر بستگی دارد:
:: کیفیت دوغاب و فرمول بدنه و خصوصاً پلاستیسیته آنها و دانسیته و وسیکوزیته و دانه بندی دوغاب.
:: نوع اسپری درایر
:: نوع نازلهای پاشنده و تعداد و انداز سوراخ و آرایش آنها
:: جنس نازلها و سایر اجزاء نازل
:: ابعاد محفظه
:: کیفیت پمپاژ و فشار پمپ
:: رطوبت پودر و دانه بندی پودر
:: استحکام پودر و هموژن بودن رطوبت آنها
:: ماندگاری پودر
:: حرارت داخل محفظه، فشار داخل محفظه و میزان رطوبت محفظه
:: ثبات فشار گاز
۳- مرحله شکل دهی یا پرس پودر:
اساس این روش به طور ساده بدین ترتیب است که مخلوط مواد اولیه به صورت پودر با دانه بندی مناسب در حفره های قالب قرار گرفته و تحت فشار قرار میگیرد. بدین ترتیب مواد اولیه شکل حفره را به خود میگیرد. رطوبت پودر مورد استفاده حدوداً پنج درصد و دانه بندی پودر مشخص و باید ثابت باشد. امروزه در صنایع تولید کاشی، پرسهای بسیار مدرن و با توانمندیهای بالا وجود دارد که حتی میتوان طرح را در مرحله پرس کردن اعمال نماید (به عنوان مثال طرحهای vein در کاشیهای گرانیتی) و قالبهای رستیک در کاشیهای کف و دیوار و پرسلان قسمت پرس در کارخانجات تولید کاشی به عنوان یکی از مهمترین قسمتها بوده و علت آن برمی گردد به اینکه در این قسمت کلاً ماده ای با یک ماهیت پودری به بدنه کاشی تبدیل میشود و این تغیر ماهیت با مشکلات زیادی همراه میباشد، نظیر: