فولادهای عملیات حرارتی پذیر چیست؟
فولادهای عملیات حرارتی پذیر، گروهی از فولادها هستند که با اعمال عملیات حرارتی، مانند سخت کاری، می توان خواص مکانیکی آن ها را بهبود بخشید. این فولادها، کاربری ویژه ای ندارند، اما در صنایع قطعه سازی و ماشین سازی، به دلیل استحکام، سختی و مقاومت سایشی بالا، کاربرد گسترده ای دارند. خواص اصلی این فولادها عبارتند از:
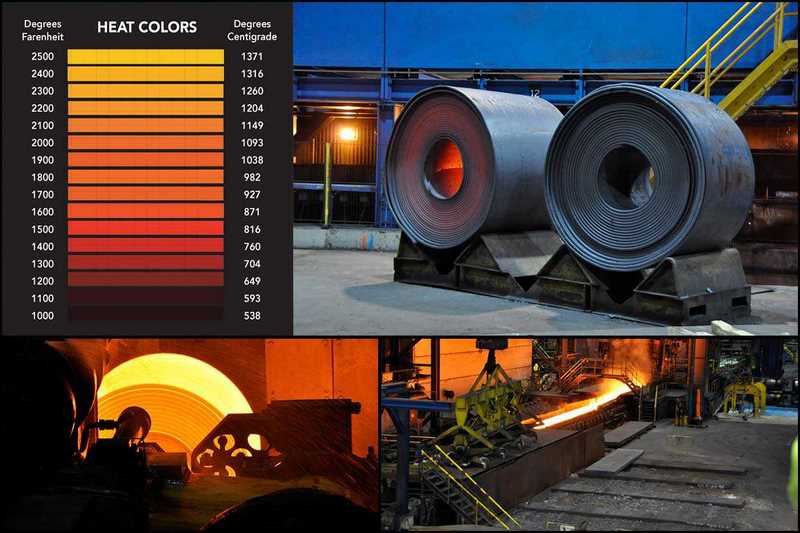
- سختی پذیری و عملیات حرارتی پذیری عالی
- قابلیت عملیات حرارتی القایی
- چقرمگی بالا
- انعطاف پذیری
- قابلیت فورج و نوردپذیری مطلوب
- استحکام متوسط به بالا
- مقاومت سایشی و خستگی مناسب
همچنین، فولادهای عملیات حرارتی پذیر، به دلیل قابلیت سخت کاری، می توانند سختی و استحکام بالایی داشته باشند. این قابلیت، باعث کاربرد گسترده این فولادها در صنایع مختلف، به خصوص قطعه سازی و ماشین سازی شده است. دمای سخت کاری، دمای کوئنچ کردن فولاد است. نوع سخت کاری، روشی است که برای افزایش سختی و استحکام فولاد استفاده می شود. همچنین سختی، میزان مقاومت فولاد در برابر سایش و خراش است.
انواع فولاد عملیات حرارتی پذیر در این قسمت به انواع فولادهای رایج در عملیات حرارتی پذیر اشاره میکنیم و توضیح مختصری درباره هریک از این نوع فولادها ارائه میدهیم. شما میتوانید با توجه به قیمت روز آهن آلات و نیاز خود و حوزهای که در آن فعالیت میکنید، فولاد عملیات حرارتی پذیر موردنظر خود را انتخاب و اقدام به خرید کنید. این نوع فولادها کاربرد گسترده و مهمی در ساخت محور، میل لنگ، چرخ دنده، شافت، پین، شاتون، پیچ و مهره دارند. همچنین در قطعات انواع ماشین آلات و وسایل تقلیه نیز از این فولادها استفاده میشود.
1.فولادهای عملیات حرارتی پذیر غیر آلیاژی فولادهای عملیات حرارتی پذیر غیر آلیاژی، فولادی هستند که تنها حاوی مقادیر کمی کربن و عناصر آلیاژی هستند. این فولادها معمولاً دارای سختی و مقاومت تسلیم نسبتاً پایینی هستند، اما چقرمگی و شکلپذیری خوبی دارند. از فولادهای عملیات حرارتی پذیر غیر آلیاژی در ساخت قطعاتی استفاده میشود که تحت بارهای دینامیکی و ضربه قرار میگیرند، مانند چرخدندهها، محورها و قطعات ماشینآلات.
2.فولادهای عملیات حرارتی پذیر منگنز دار فولادهای عملیات حرارتی پذیر منگنز دار، فولادی هستند که حاوی مقادیر قابل توجهی از منگنز (1.5 تا 3 درصد) است. منگنز باعث افزایش استحکام و مقاومت به سایش این فولادها میشود. از فولادهای عملیات حرارتی پذیر منگنز دار در ساخت قطعاتی استفاده میشود که تحت بارهای سنگین و سایش قرار میگیرند، مانند چرخدندههای سنگین، میل لنگها و قطعات ماشینآلات سنگین.
3.فولادهای عملیات حرارتی پذیر کروم دار فولادهای عملیات حرارتی پذیر کروم دار، فولادهایی هستند که حاوی مقادیر قابل توجه کروم (1.5 تا 3 درصد) میشوند. کروم باعث افزایش مقاومت به خوردگی و زنگزدگی این فولادها میشود. از فولادهای عملیات حرارتی پذیر کروم دار در ساخت قطعاتی استفاده میشود که در معرض محیطهای خورنده قرار میگیرند، مانند لولههای نفت و گاز، مخازن و تانکرها.
4.فولادهای عملیات حرارتی پذیر کروم-مولیبدن دار فولادهای عملیات حرارتی پذیر کروم-مولیبدن دار، فولادهایی هستند که حاوی مقادیر قابل توجهی کروم (1.5 تا 3 درصد) و مولیبدن (0.2 تا 0.4 درصد) هستند. کروم و مولیبدن باعث افزایش مقاومت به خوردگی و سایش این فولادها میشود. از فولادهای عملیات حرارتی پذیر کروم-مولیبدن دار در ساخت قطعاتی استفاده میشود که تحت بارهای سنگین و شرایط سخت محیطی قرار میگیرند، مانند توربینهای گازی، قطعات هواپیما و تجهیزات نظامی.
انواع فولادهای عمیلاتی حرارتی پذیر در شرکت نورد عملیات حرارتی چیست ؟ عملیات حرارتی فولادها شامل حرارت دادن به آنها تا دمایی مشخص (بالا یا پایینتر از دماهای بحرانی)، نگهداری فولاد در آن دما و نیز سرد کردن با سرعتی مشخص و کنترلشده بهمنظور دستیابی به ریزساختار و خواص موردنظر است. درواقع، با انجام عملیات حرارتی، این امکان فراهم میشود که بدون تغییر در ترکیب شیمیایی و تنها از طریق گرم و سرد کردن قطعه، به خواص مناسب و مطلوب دستیابیم.
باوجوداینکه این فرآیند را عموماً با حرارت دهی به قطعه در کوره میشناسند، اما در طی انجام فرآیندهایی نظیر شکلدهی گرم، جوشکاری و لحیمکاری، نوعی عملیات حرارتی بر روی قطعه انجام میگیرد. چون در این فرآیندها، درجه حرارت بالایی به قطعه اعمال میشود که منجر به تغییر ریزساختار در اطراف منطقه حرارت دیده میشود. با سرد شدن قطعه پس از فرآیندهای یادشده، سیکل عملیات حرارتی در این نوع فرآیندهای شکلدهی و اتصال تکمیل میشود.
آنیل کردن فولاد ها به هر نوع عملیات حرارتی که منجر به تشکیل ساختاری بهجز مارتنزیت (مارتنزیت یک فاز سخت و شکننده و عامل افزایش سختی در فولادهاست که با حرارت دادن و سریع سرد کردن ایجاد میشود) و با سختی کم و انعطافپذیری زیاد شود، آنیل یا بازپخت میگویند. عملیات آنیل کردن یا بازپخت، خود طیف وسیعی از عملیات حرارتی را شامل میشود که اغلب برای کاهش سختی و یا حذف تنشها به کار برده میشود. فرآیندهای آنیل برحسب دمای عملیات، روش سرد کردن، ساختار و خواص نهایی به انواع مختلفی تقسیم میشوند. مهمترین عملیات آنیل شامل موارد زیر میشوند:
- آنیل کامل
- آنیل هم دما
- آنیل جزئی
- آنیل کروی
- آنیل نفوذی یا آنیل یکنواخت
آنیل کامل با اعمال حرارت در طی این فرآیند، فولاد وارد فاز آستنیت ( آستنیت فازی از آهن است که در گستره دمایی 727 تا 1493 درجه سانتیگراد پایدار است) میشود و پس از سرمایش نیز ساختاری فریتی-پرلیتی خواهد داشت (فریت یک فاز از آهن است که تا زیر دمای 723 درجه سانتیگراد پایدار است). حاصل چنین فرآیندی بر روی فولادها، ایجاد ساختار دانهریز و یکنواخت، کاهش سختی، حذف تنشهای داخلی و بهبود قابلیت ماشینکاری است. اگر واژه “آنیل” بدون پسوند استفاده شود، منظور همان آنیل کامل است.
آنیل هم دما ضمن اینکه، مشابه با آنیل کامل، ریزساختار حاصل برای فولادهای هیپویوتکتوئیدی شامل فریت-پرلیت ، برای فولادهای یوتکتوئیدی شامل پرلیت و برای فولادهای هایپریوتکتوئیدی شامل پرلیت-سمنتیت است. با این تفاوت که پرلیتها ظریفتر و درصد فریت و سمنتیت کمتر است. نرماله کردن فولاد ها یکی از مهمترین اهداف نرماله کردن، ریز کردن دانههای درشتی است که اغلب در هنگام کار گرم در دمای بالا یا در ضمن ریختهگری و انجماد ایجاد میشوند. به دلیل کاهش فاصله بین لایههای پرلیت (پرلیت شامل ساختاری لایهای از فریت و سمنتیت است) در نرماله کردن فولاد،
کروی کردن فولاد ها عملیات حرارتی بازیابی فولاد ها انجام کار سرد بر روی فولادها باعث افزایش استحکام و سختی و کاهش انعطافپذیری آنها میشود. این پدیده به کارسختی موسوم است که ناشی از افزایش پیوسته معایب بلوری است. از طریق عملیات حرارتی بازیابی، معایب بلوری در ساختار بلوری فلز از بین رفته یا کاهش مییابند. در این فرآیند، خواص فیزیکی بهطور کامل بازیابی میشود و مشابه با خواص فیزیکی قطعه قبل از کار سرد میشود اما خواص مکانیکی تغییرات چندانی نمیکند. عملیات حرارتی تبلور مجدد فولاد ها ازجمله اثرات کار سرد،
تمپر کردن فولاد ها کوئنچ کردن فولاد کوئنچ کردن یا سریع سرد کردن مستقیم، نوعی عملیات حرارتی بهمنظور سخت کردن قطعه فولادی است. این فرآیند مستلزم سریع سرد کردن فولاد از دمای آستنیته شدن تا زیر دمای Mf (دمای پایان مارتنزیت شدن) است. در فرآیند کوئنچ کردن فولادها، سطح و مغز قطعه با یک سرعت مشابه سرد نمیشوند و درنتیجه، تشکیل فاز مارتنزیت در نواحی یادشده بهطور همزمان نخواهد بود. از اثرات این فرآیند میتوان به ایجاد تنشهای داخلی و درنهایت شکست یا تغییر شکل قطعه اشاره کرد. دیگر عملیاتهای کوئنچ کردن در فولادها شامل مارتمپرینگ یا مارکوئنچینگ و آستمپرینگ میشوند.
بدین منظور از عملیات حرارتی سخت کردن سطحی استفاده میشود. سخت کاری سطحی فولادها برحسب اینکه منجر به تغییر در ترکیب شیمیایی سطح فولاد میشود یا خیر، به دو دسته تقسیم میشود. عملیاتی که منجر به تغییر در ترکیب شیمیایی سطح میشوند به عملیات ترموشیمی و نوع دوم که ترکیب شیمیایی سطح را تغییر نمیدهند به عملیات حرارتی موضعی معروفاند. عملیات ترموشیمی با افزودن برخی عناصر آلیاژی از طریق نفوذی به ساختار فولادها، افزایش سختی را برای آنها به همراه دارد. را در این لینک بخوانید. ضمن اینکه، سخت کاری موضعی اغلب برای سطوحی که کربن کافی دارند انجام میشود.
- کربن دهی
- نیتروژن دهی
- بور دهی
- کربن- نیتروژن دهی
- سیانید دهی
انواع فرآیندهای سخت کاری سطحی بدون تغییر در ترکیب شیمیایی سطح نیز عبارتاند از:
- سخت کاری شعلهای
- سخت کاری القایی
عملیات حرارتی فولاد ها در یک نگاه در شکل زیر که یک نمودار فازی آهن- کربن است، علاوه بر دماهای بحرانی، محدوده دمایی مهمترین عملیات حرارتی فولادها نیز مشخص شده است. انواع روش های سرد کردن در عملیات حرارتی سومین مرحله از عملیات حرارتی یک قطعه، سرد کردن آن است. این مرحله مستلزم انتخاب محیط سردکننده مناسب است. چراکه سرعت سردسازی به نوع محیط وابسته است. این امر از طریق پارامتر H که شدت سردکنندگی محیط است، نشان داده میشود.
انواع محیطهای سرد کردن در عملیات حرارتی عبارتاند از: در بین موارد گفتهشده، آبنمک شدت سردکنندگی بیشتری دارد و قطعاتی که در آبنمک سرد میشوند، ساختاری شامل مارتنزیت بیشتر خواهند داشت. پس از آبنمک نیز به ترتیب آب، روغن و هوا دارای سرعت سرد شدن بالاتری هستند. سختی پذیری فولاد ها سختی پذیری بهصورت توانایی یا قابلیت تشکیل مارتنزیت و سخت شدن فولاد در اثر سریع سرد شدن از ناحیه آستنیت تعریف میشود. ضخامت پوسته سخت شده نیز به فاصله سطح تا محلی در داخل قطعه که دارای 50 درصد مارتنزیت است، گفته میشود. پارامترهای مؤثر بر روی سختی پذیری عبارتاند از:
- اندازه دانههای آستنیت
- درصد کربن
- عناصر آلیاژی
- آخالها و ناخالصیهای فلزی
- همگن بودن ریزساختار